Today’s highly available precision roller screws are cost-effective enough to be effective solutions for even budget-conscious applications.
Planetary roller screws provide significant benefits over other screw-type actuators in terms of performance, load capacity, duty cycle, and lifetime. Traditionally, however, those benefits have come along with significantly higher prices and lead times. As a result, the technology was typically saved for applications that had to have performance, no matter what the price. Now, Tolomatic, a manufacturing partner of Motion Solutions, has released a family of US-made roller screws. With dramatically reduced pricing and lead times of as little as two weeks, the product line enables engineers designing general industrial automation equipment to gain the performance advantage of roller screws. For OEMs with specialized applications or who need to replace a product from a previous vendor, Motion Solutions can team with Tolomatic to customize a roller screw, and they can do it more economically and quickly than ever before.
Planetary roller screws 101
A planetary roller screw combines characteristics of a standard screw-type actuator with the configuration of a planetary gearbox. Many variations exist but the most general type consists of a nut that travels relative to the screw. Instead of recirculating balls, the interface between the threaded nut and the screw consists of a series of rollers arranged around the screw in a planetary fashion. The nut threads mesh with the roller threads, and the roller threads mesh with the threads of the screw (see figure 1).
Roller-Screw-cutaway
In a planetary roller screw, the nut is lined with a planetary arrangement of rollers. The rollers reduce friction while significantly increasing contact area, enabling roller screws to support greater loads, higher duty cycles, longer lifetimes, and better accuracy and repeatability than other screw-type actuators. (Courtesy of Tolomatic)
The design significantly increases surface contact. As a result, a planetary roller screw can handle a much higher load in a smaller package than a ballscrew, for example. This characteristic makes them very effective in applications with size or weight limitations. Roller screws are also much more robust than competing technologies, enabling them to handle very high duty cycles and achieve long lifetimes.
Planetary roller screws deliver high accuracy and repeatability. They may carry a somewhat higher price than competing technologies, but it is important to make an apples-to-apples comparison. “You can get that level of performance from a ball screw, but you have to go to the next level, with precision grinding, special pre-loading, or other options,” says Aaron Dietrich, director of marketing at Tolomatic. “With a roller screw, it’s kind of inherently built in.”
The downside of that higher surface contact area is increased heat generation, greater complexity, and higher cost. To further complicate matters, the lead times for roller screws have often extended to three or four months. As a result of these factors, planetary roller screws have traditionally been reserved for specialty applications with performance demands that can only be satisfied by roller screws. They would be more likely to show up in an aerospace application than a machine for stacking auto body parts, for example. With the entry of Tolomatic into this market, that is no longer the case. Design engineers are free to apply the robust and precise performance of a planetary roller screw to a wide range of industrial applications.
Designed for cost-effectiveness
For years, Tolomatic has built actuators incorporating roller screws. Once the company began to develop high-quality roller screws to meet its in-house actuator needs, it was a short step to releasing those products to the market. From the start, Tolomatic designed its manufacturing process to yield cost-effective components on short lead time. They chose automation whenever possible, for example. “Tolomatic has made a large investment in automating the manufacturing of roller screw components to meet cost goals, increase efficiency, reduce lead times, and ensure high quality,” says Dietrich.
The next part of the recipe is to maintain inventory of screws so that products can be assembled efficiently. “As an actuator company, we support a 15-day lead time with standard actuator products including with roller screws,” says Dietrich. “As a result, we actually stock fixed lengths of roller screw at any given point in time. So, not only is the manufacturing process efficient and cost-effective, but for the most part, we have the parts for our stock components sitting on the shelf.”
Improved availability
The entry of Tolomatic into the roller screw market has come as welcome news to the industrial market. Only a small number of suppliers worldwide produce these precision components, and there is limited overlap among product lines in terms of mechanical characteristics like flanges, hole patterns, etc. If a component becomes unavailable, the chances of finding an exact drop-in replacement from a different manufacturer are slim to none.
That was the problem faced by a tier-one semiconductor test equipment manufacturer when the roller screw currently used in their platform was discontinued. They had a serious supply-chain issue, not only for the assembly of new machines but for the maintenance of existing equipment. Fortunately, the manufacturer could turn to Tolomatic and Motion Solutions for help.
Motion Solutions worked closely with Tolomatic to modify one of their roller screw products to make it a drop-in replacement. The fact that both Tolomatic and Motion Solutions are based in the United States made it possible to collaborate on the project to deliver a solution that fit, performed to specifications, and was completed in a matter of weeks.
The Motion Solutions manufacturing team examined the customer’s current product and then reviewed Tolomatic offerings. Tolomatic handled the customization of the screw shaft and the nut, and developed a lubrication solution. Motion Solutions modified the component so that it would integrate into the machine without the customer making any changes on their end. Once everything was approved, Motion Solutions built the subassemblies and shipped them directly to the customer.
Customization can be extremely useful for OEMs but success hinges on properly defining the scope. Some changes, such as adding a flange or changing the length of the lead screw, are straightforward. Others, like changing the lead of the screw, involve retooling robotic equipment and can take many months to get right. In any case, it takes volume to make the exercise practical. For a project of the right scope, though, working with a team like Tolomatic and Motion Solutions can result in a roller screw that arrives expertly assembled and ready for use.
With a low-cost, highly available roller screw product line that is built in the United States, the rules of thumb for when to use a roller screw have changed. Machine builders have a new set of solutions they can use to increase performance, meet goals, and differentiate their product in the marketplace.
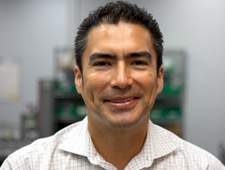
About the Author
Bill Saunders is the Vice President of Sales, Motion Solutions.